Porqué la solución de CAD/CAM de corte Alma es la referencia en la construcción naval
Publicado en 03/02/2021
Alma empieza a interesarse por el sector de la construcción naval en 1982. En esa época, Les Chantiers de l’Atlantique de Saint-Nazaire estaban buscando una solución que les permitiera minimizar sus pérdidas de material, ya que esto podía representar un importante ahorro de material, teniendo en cuenta las toneladas de acero que se necesitan para construir un buque. Alma fue creada para responder a esta demanda, y para promover en el sector industrial algoritmos de nesting automático, desarrollados en el marco de un proyecto de investigación en la Universidad de Grenoble. Así es como comienza una larga cooperación con los astilleros de Saint-Nazaire, pero fue también el punto de partida del desarrollo y despliegue de nuestros softwares de CAD/CAM de corte para la construcción naval en el mundo entero. Hoy, nuestros softwares nos permiten responder a todas las demandas específicas de la construcción de buques y también a ser reconocidos como el principal actor en el CAD/CAM naval aplicada a la chapistería.
Además de tener que utilizar buenos algoritmos de nesting automático, ¿cuáles son las características del trabajo en la construcción naval? O precisamente, ¿qué debe ofrecer una buena solución de CAD/CAM para el sector naval? La respuesta es múltiple.
Integrar la lógica de fabricación de un buque
Ante todo, lo importante es entender cómo se construye un buque, ya que de ello depende la organización de los datos (piezas para cortar y stock de chapas y de retales). Un buque está formado de bloques, ensamblados progresivamente partiendo desde el centro por una cuestión de equilibrio. Cada bloque está formado de sub-ensamblajes, compuestos a su vez de paredes y suelos; por lo que generalmente, los datos deben estar organizados por bloque, para no mezclar piezas provenientes de bloques diferentes en un mismo posicionamiento de piezas. Efectivamente, debemos evitar de complicar la logística -ya muy exigente- y simplificar la clasificación de piezas cortadas para enviarlas directamente a los sub-ensamblajes en donde se van a soldar. Por lo general, el material necesario se calcula antes de terminado el diseño detallado del buque, basándose en las primeras versiones de piezas provenientes del CAD; este material va a la reserva de chapas necesarias para cada bloque, aunque, a veces, los retales recuperables pueden intercambiarse con otros bloques.
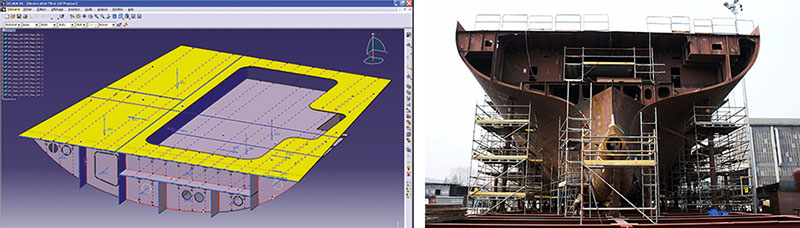
Recuperar los datos geométricos y de mecanizado
En nuestros primeros proyectos navales, empezamos definiendo un formato neutro de intercambio de datos con el CAD. Después, con el tiempo, fuimos desarrollando las interfaces con todos los sistemas del sector, por lo que, en el día de hoy, podemos trabajar con cualquier astillero equipado con el CAD que prefiera. Primero importamos las geometrías que describen las piezas a cortar, separándolas si es necesario en el caso de un DXF de piezas múltiples, y luego, recuperamos todos los datos de mecanizado que más se utilizan. Pueden ser los diferentes procesos de marcado y de amoldadura, la gran variedad de textos que indican el nombre de reforzadores de soldadura, los ejes del buque, las líneas de plegado, las propiedades de chaflán para cada arista, etc. Sin embargo, cabe saber que más allá de la importación de la geometría y del mecanizado de una pieza, cuando desplegamos nuestra solución, casi sistemáticamente debemos adaptar el proceso de importación/exportación de las piezas, al proceso y a la manera de trabajar del astillero. Por ejemplo, ¿cómo se debe tratar la modificación de una pieza?, ¿debemos anular sistemáticamente los posicionamientos de la pieza modificada, o dejar que lo haga el usuario?
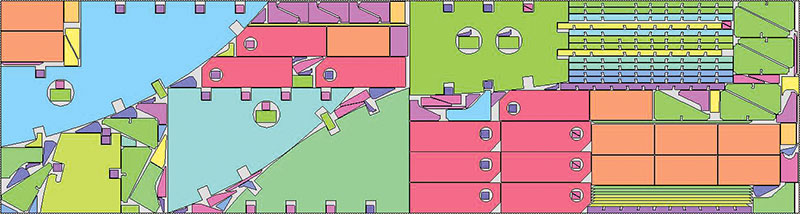
Dominar perfectamente el corte por plasma, el corte de chaflanes y el marcado
Para cualquier solución de CAD/CAM naval se deben tener en cuenta las particularidades relacionadas a la actividad y a las máquinas que generalmente se utilizan. Por lo que dominar el corte por plasma (la técnica más utilizada debido al espesor de las chapas que se cortan) es fundamental. Entre las funcionalidades más utilizadas encontramos el corte continuo (piezas anidadas juntas para minimizar la cantidad de ataques y, por lo tanto, reducir el tiempo de mecanizado), la gestión de las uniones (dejar algunas aperturas atadas a la pieza para facilitar el transporte) o el corte del esqueleto (para facilitar la evacuación). En la actividad de la construcción naval, también se deben saber utilizar máquinas chaflaneadoras y saber dirigir las operaciones relacionadas (multipaso, control de altura, bucles de reparametrado, etc.) y las unidades de marcado especiales. Estas últimas permiten, sobre todo, marcar todo tipo de texto que sirva para ensamblar o soldar las piezas.
Manejar máquinas (muy) especiales
La principal razón de nuestro éxito en el sector naval, es nuestra capacidad para manejar máquinas especiales, y para ello, ofrecer una solución lo suficientemente abierta que permita utilizar funcionalidades de base del software de CAD/CAM para desarrollar aplicaciones totalmente específicas. Por ejemplo, sabemos utilizar las líneas de máquinas de “paneles planos”. Estas sirven para ensamblar y soldar chapas en las que se pueda cortar una gran pieza para un puente de buque, y al final, soldar los perfiles o refuerzos que aseguren su rigidez y planitud. El corte se realiza en una máquina que permite efectuar, además, otras operaciones como la amoldadura, el marcado, el trazado de textos y el chanfleado. Otro ejemplo de máquinas especiales que nuestro software maneja, son las máquinas “simétricas”. Ya sea las que permiten marcar/cortar al mismo tiempo piezas babor y estribor “casi” idénticas, o las máquinas “de dos cabezales asincrónicos” para cortar al mismo tiempo, la parte de abajo y de arriba de una misma pieza, sin que las aristas cortadas sean estrictamente paralelas.
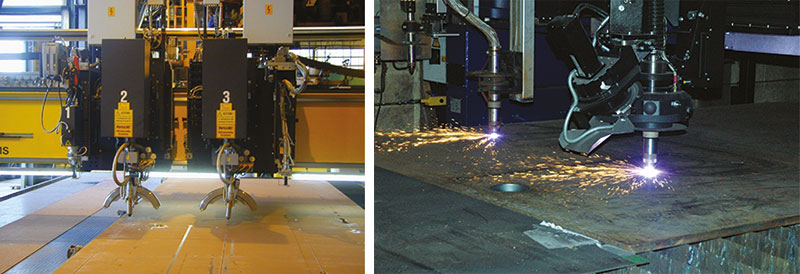
Automatizar el funcionamiento del software
Una de las características de la construcción naval es la gran cantidad y variedad de piezas que se deben anidar y cortar. Esto nos permite optimizar nuestros algoritmos de nesting automático y, más en general, nos impone un funcionamiento lo más automatizado posible para reducir a la vez, los tiempos de programación y los riesgos de error. Por lo tanto, la gran mayoría de las soluciones que ofrecemos se articulan alrededor de las siguientes fases, que se realizan y se siguen de manera automática: importación de piezas con preparación de mecanizado, creación de órdenes de lanzamiento (agrupados por materia/espesor/bloque), nesting y generación de archivos CN en modo batch. Por último, existe una fase facultativa de cierre de las órdenes de lanzamiento que permite desplazar las piezas cortadas y utilizar los retales generados para el anidado. Cabe señalar igualmente, la personalización casi sistemática de los documentos que quedan automáticamente a la disposición de los operarios de máquinas y de los programadores, para responder, sobre todo, a la necesidad de identificar las piezas cortadas y facilitar la clasificación.
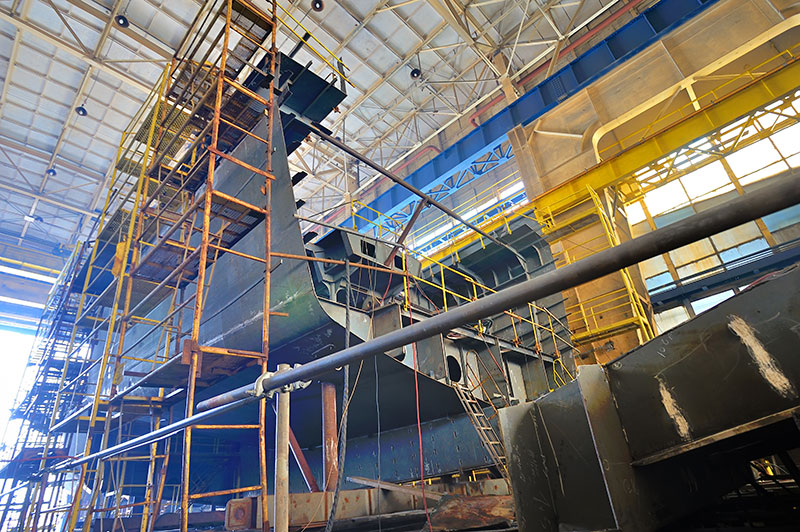
Manejar los procedimientos de corte lineal y de soldadura robotizada
Como se ha dicho anteriormente, un buque está formado de chapas y perfiles ensamblados mediante soldadura; los perfiles sirven principalmente a darle rigidez a la estructura del buque. Las “tripas” (cables y tubos) se colocan a nivel de los subensamblajes o de los bloques. La obra muerta (equipo interior) se instala lo antes posible, pero después del ensamblado de los primeros bloques. En todo este proceso, nuestros softwares intervienen, no solamente para el nesting y para cortar las piezas de metal, pero también para optimizar el corte de los perfiles. También hemos desarrollado diferentes algoritmos de nesting de los perfiles para maximizar la utilización de las barras de materia prima, respetando al mismo tiempo, las características de las máquinas (sierra o robot) que manejamos. Además, para ampliar nuestros conocimientos, nos interesamos por las problemáticas de soldadura específicamente relacionadas con el sector naval. Nuestro software Almacam Weld, cuenta con numerosas funcionalidades automáticas de reconocimiento geométrico de modelo en 3D y de generación de tareas de soldadura, y nos permite responder a las exigencias de programación fuera de línea de robots de soldadura.
Un espíritu de colaboración fuerte y una lógica de servicio en todas partes del mundo
Además de las capacidades técnicas de nuestras soluciones de software, la notoriedad de Alma se debe a la experiencia y conocimientos acumulados gracias a la relación de confianza con nuestros clientes y a colaboraciones sólidas con diferentes actores del sector naval; sobre todo, los editores de soluciones de CAD/PLM. Esta sólida experiencia de casi 40 años se fue construyendo progresivamente y se ha transmitido al conjunto de los equipos comerciales y técnicos de nuestra red. Todo esto nos permite iniciar con confianza y serenidad cualquier proyecto naval en el mundo, ya que dominamos las problemáticas generales de la construcción naval, así como las particularidades relacionadas a los diferentes tipos de buques o a la localización del astillero. Los constructores europeos de buques de crucero más grandes confían en nosotros y equipamos a gran cantidad de constructores de buques militares o de transporte de mercancía en todo el mundo (Brasil, Estados Unidos, Francia, Italia, Alemania, China, India, Indonesia, Corea, Japón, etc.).
Por último, apostamos en nuestra nueva gama de productos Almacam para ofrecerles a nuestros clientes más valor añadido. Esta nueva versión que estará disponible para el sector naval dentro de un año, ofrecerá, sobre todo, una trazabilidad completa de la fabricación, funcionalidad ineludible para controlar los procesos de calidad que se aplican hoy en día.